Demand for High Quality Lost Foam Casting Manufacturers in India is Growing Rapidly
The recent years have seen India emerging as a competitive hub for high-quality lost foam casting producers. The requirement of accuracy, efficiency, and affordability in metal casting enterprises has increased the demand for advanced technology, led by lost foam casting. Sectors such as automotive, agriculture, defence, and engineering increasingly look towards lost foam casting due to its dimensional accuracy and reduced finishing costs. It is quickly driving the increase of trustworthy manufacturers all around India.
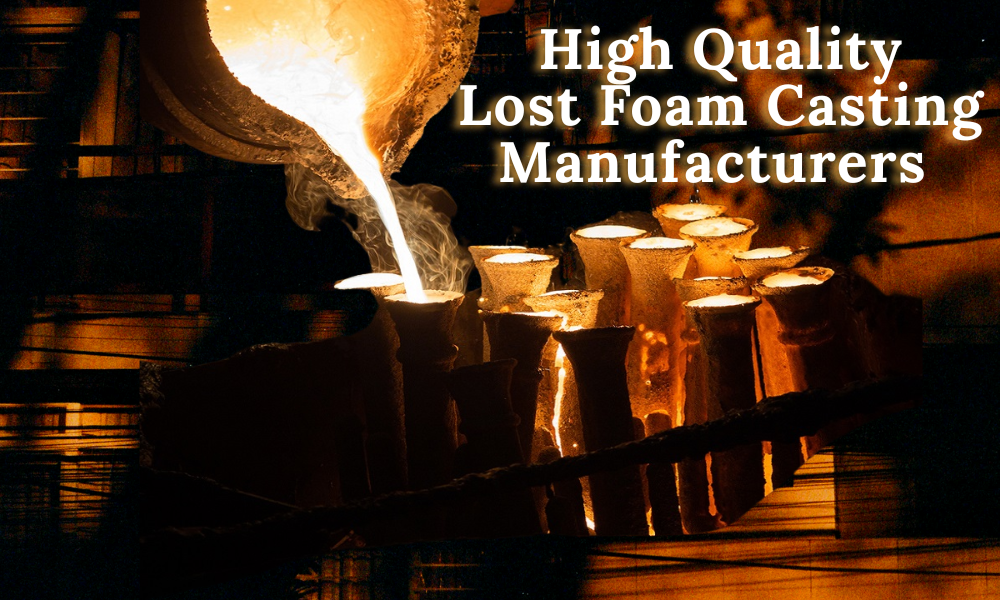
Understanding Lost Foam Casting
Lost foam casting is a modern process of metal casting in which a polystyrene foam pattern of foam is used to create the mold cavity. The foam pattern is covered in a refractory coating and subsequently covered in unbonded sand. As molten metal is poured over it, the foam is destroyed by vaporization and is filled by the metal, resulting in a near-net-shape casting with great accuracy.
The method greatly minimizes the steps involved in conventional casting operations and does away with the cores or parting lines. Owing to these benefits, lost foam casting is a clean, efficient and green way of casting.
Why the Demand for Lost Foam Casting is Increasing in India
There are a number of reasons why demand for high-quality lost foam casting manufacturers in India is picking up:
- Booming Automotive and Engineering Sectors: India’s automotive and general engineering sectors are experiencing strong growth. These industries require lightweight, strong, and sophisticated metal components, and lost foam casting efficiently produces the same. Ranging from cylinder heads to engine blocks and suspension arms, lost foam casting is increasingly being favored over traditional means on account of its higher dimensional accuracy.
- Focus on High Precision Components: The Indian manufacturing ecosystem is shifting direction towards global standards. Organizations now demand cast pieces with tighter tolerances, less machining requirements and smoother finishes. Lost foam casting delivers all of these, thus becoming a favourite technique among OEMs and Tier-1 suppliers.
- Cost and Time Efficiency: Lost foam casting significantly minimizes post-processing, machining time and wastage of material. In the wake of increasing global competition, Indian industries are looking for cost effective manufacturing processes. This has led to a huge push for suppliers who can supply lost foam casting at scale at no compromise on quality.
- Government Push for Manufacturing Excellence: Initiatives such as ‘Make in India’ and higher investment in infrastructure and industrialization within the country have propelled growth in the foundry industry. Lost Foam Casting Supplier in India foundries are, therefore, going in for newer, cleaner, and more accurate processes like lost foam casting to address local and export requirements.
- Sustainability and Environmental Benefits: Lost foam casting generates less emission and generates less industrial waste than conventional sand casting or die casting methods. Manufacturers are now compelled to adopt cleanerand greener manufacturing methods especially with more environmental regulations and global supply chain sustainability objectives.
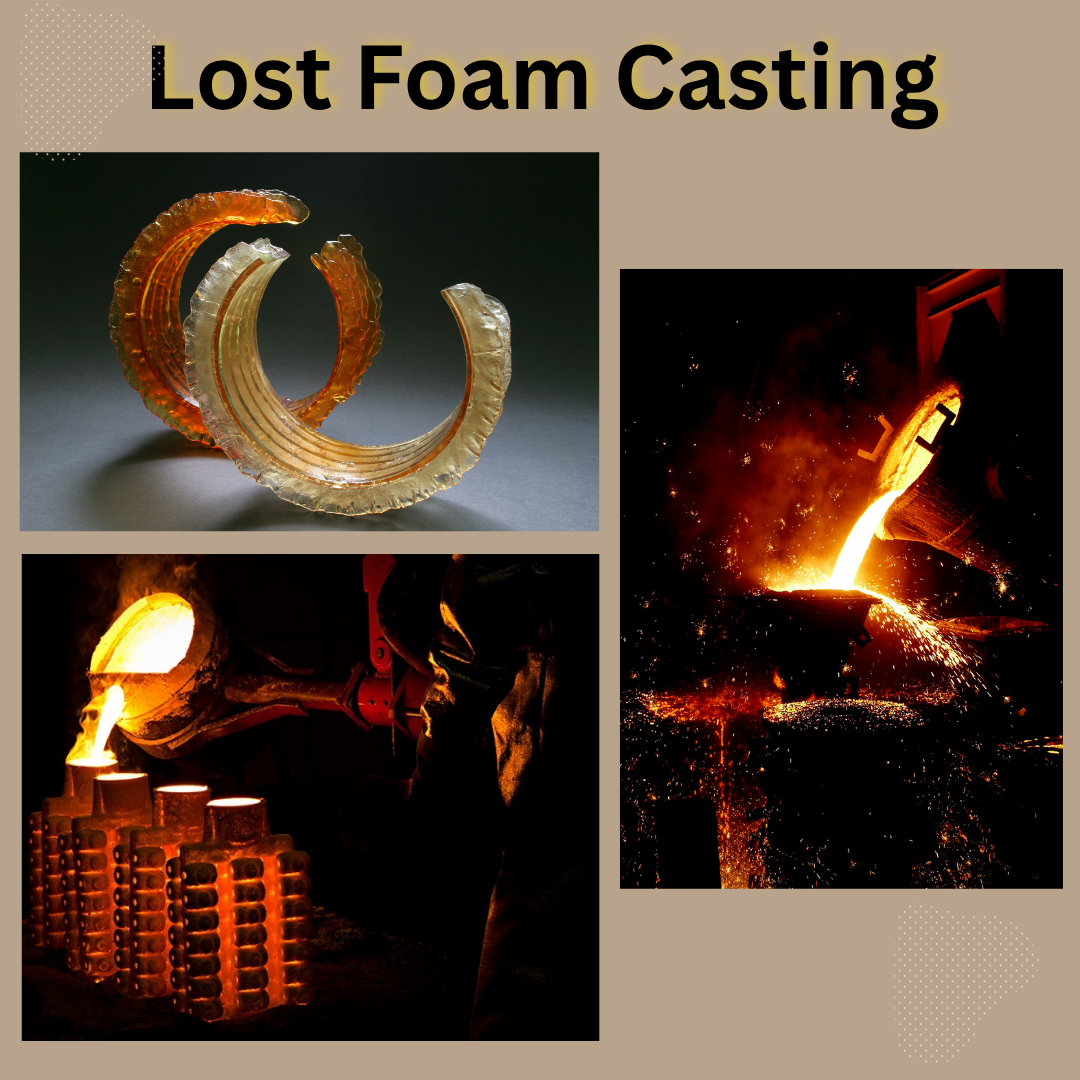
Key Applications Driving the Demand
- Automotive Industry: Lost foam casting is greatly utilized in the automotive industry for manufacturing intricate engine components, gearboxes, and other parts. Thin-walled sections and complex geometries can be easily casted, making it a prime reason why the automotive industry is moving toward this process.
- Aerospace and Defence: For industries where reliability and precision are non-negotiable to compromise on, lost Foam Casting in India guarantees consistency in parts. Advanced aerospace and defence parts are being procured from Indian manufacturers in large numbers because they are cost efficient and can deliver on quality standards.
- Agricultural Equipment and Heavy Machinery: Farm machinery and earth moving machinery components often require robust, complex, and light castings. Lost foam casting is a reliable tool or solution for bulk production and customized orders for such industries.
- Industrial Pumps and Valves: Production of pump impellers, housings, valve bodies, and other industrial parts using lost foam casting provides better surface finish and reduced machining requirements. These advantages are now luring industrial equipment producers to Indian lost foam casting suppliers.
Growth of High-Quality Manufacturers in India
The situation today is observing highly advanced lost foam casting production units, particularly in industry centres such as Rajkot, Coimbatore, Pune, and Faridabad. These businesses have incorporated global quality management systems, modern molding lines and CNC based inspection equipment.
A few of the salient indicators of the increase in quality among Indian manufacturers are:
• Implementation of sophisticated EPS pattern making machines
• Robot based coating and drying chambers
• Totally automated sand handling system
• In-house metallurgical testing and non-destructive testing (NDT) labs
• Capacity to process small batch and high-volume orders
Additionally, Indian manufacturers today export to nations like the US, Germany, and Japan, thereby competing with them globally in both price and quality. Lost Foam Casting Companies in India are making a mark in competitive global markets.
What to Seek in a Qualified Lost Foam Casting Producer?
For industries and consumers interested in procuring components through lost foam casting, some essential points to look for when choosing a producer include:
• Experience in your specified industry application
• Certifications like ISO 9001, TS 16949, or AS9100
• Up-to-date infrastructure and machine controlled(automated) process
• Ability to produce complex designs with minimal porosity
• Consistent quality control and delivery performance
Choosing the right manufacturer is important to ensure optimal cost-efficiency and to meet the functional performance of cast components.
Conclusion
India is fast turning into a world leader in lost foam casting production. As the demand for high precision, light weight, and affordable components in various industries continues to grow India’s high quality lost foam casting producers are stepping up to international standards. The blend of technology, talent pool, and infrastructure growth is taking center stage in this process. For businesses intending to tap into high-end casting services,India is an emerging hot spot.
The future of lost foam casting in India is promising with increased manufacturers improving their capacity and industries embracing the economic and environmental advantages of this advanced casting method.